Cambridge Sustain 8
Build a foundation for significant sustainability improvement in eight simple steps.
Cambridge Sustain 8 is an organisational engagement programme focused on making significant sustainability improvements with minimal investment. By bridging the gap between corporate objectives and sustainable practices on the factory floor, this approach has been successfully implemented in numerous factories, yielding measurable savings within just one year of implementation.
Build a foundation for significant sustainability improvement in eight simple steps.
Cambridge Sustain 8 is an organisational engagement programme focused on making significant sustainability improvements with minimal investment. By bridging the gap between corporate objectives and sustainable practices on the factory floor, this approach has been successfully implemented in numerous factories, yielding measurable savings within just one year of implementation.
BENEFITS OF SUSTAIN 8
Motivating sustainability KPIs: Develop sustainability Key Performance Indicators (KPIs) that inspire and drive continuous improvement.
Visual management tools: Bring data to life through visual management tools, enhancing understanding and decision-making.
Transparent organisational reporting: Track and report progress towards sustainability goals, ensuring transparency and accountability.
Engaging frontline staff: Involve frontline employees in the development of improvement plans, harnessing their expertise and commitment.
Scalable foundation for improvement: Establish a solid foundation for ongoing improvement efforts that can be replicated across multiple sites.
Targeted Waste Reduction: Rapidly establish initiatives to eliminate waste in critical areas such as energy, water, and rework.
Motivating Sustainability KPIs: Develop sustainability Key Performance Indicators (KPIs) that inspire and drive continuous improvement.
Visual Management Tools: Bring data to life through visual management tools, enhancing understanding and decision-making.
Transparent Organizational Reporting: Track and report progress towards sustainability goals, ensuring transparency and accountability.
Engaging Frontline Staff: Involve frontline employees in the development of improvement plans, harnessing their expertise and commitment.
Scalable Foundation for Improvement: Establish a solid foundation for ongoing improvement efforts that can be replicated across multiple sites.
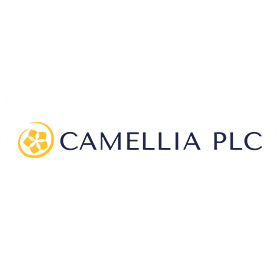
FEATURED CASE STUDY
“Since working with IfM, everything we implemented has been continued. Shop floor workers now own the energy-saving culture. Some team members have now moved to other factories and are implementing these ideas in these factories. So, the ideas and what we have learnt are spreading. We’re working together effectively and committed to bringing our customers tea that has a minimal impact on the environment.”
Chris Ballard, EPK’s Technical Director, Eastern Produce Kenya part of Camellia Plc
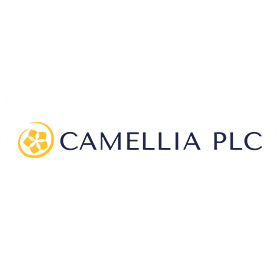
FEATURED CASE STUDY
“Since working with IfM, everything we implemented has been continued. Shop floor workers now own the energy-saving culture. Some team members have now moved to other factories and are implementing these ideas in these factories. So, the ideas and what we have learnt are spreading. We’re working together effectively and committed to bringing our customers tea that has a minimal impact on the environment.”
Chris Ballard, EPK’s Technical Director, Eastern Produce Kenya part of Camellia Plc
Three ways Sustain 8 can make an impact in your organisation

Establish a link between key business drivers and sustainability engagement on the factory floor
Many organisations have clear, strong sustainability strategies and plans, but often fail to link these to the day-to-day reality of the factory floor. Our methodology fills this gap by inspiring frontline staff to create improvement plans that resonate with their work and align them with key business drivers. This alignment is crucial for the sustained success of your sustainability initiatives.
“The shop floor teams took the project as their own and not a Cambridge University project. Engaging the staff created ownership of the process and how the process directly impacted their personal lives” Chris Ballard, EPK’s Technical Director, Eastern Produce Kenya
Focus on success: Harness the power of ‘Good Days’
Our method highlights the achievements and practices that drive success on the best days in factories. This approach serves as a powerful motivational technique, increasing engagement and dedication to the project.
“By focusing on the strengths of factories on their best days, we can identify what sets them apart and replicate these practices more frequently. This leads to significant sustainability improvements. We have witnessed the positive and motivating impact of this approach.” Gary Punter, Industrial Associate, IfM Engage
Achieve significant sustainability improvements in just 12 months
The initial steps of our engagement process focus on establishing a robust data collection plan, baselines and effective KPIs to drive improvement. Within four months, there are improvement teams set up and working on action plans across the factory. The result is that notable KPI improvements have been achieved within a year across diverse cultures and sectors.
GET IN TOUCH
Contact us to find out more about the Cambridge Sustainable Improvement Method, and how it could make a sustainable impact in your organisation.