Case study
Unlocking opportunities for specialist metals fabricator
STAINLESS METALCRAFT
Impact
£50 million | target annual turnover within 5 years
Impact
£50 million | target annual turnover within 5 years
Following a series of strategy development workshops, Metalcraft targeted and then secured a major contract for the provision of high integrity stainless steel nuclear waste storage containers for Sellafield Ltd, the company responsible for delivering decommissioning of the UK’s nuclear legacy. This contract alone will be worth £47 million over the next 10 years and is a significant step towards achieving Metalcraft’s target annual turnover of £50 million within five years.
When Austen Adams joined Stainless Metalcraft as its new Managing Director, one of his first actions was to sign the company up to the Civil Nuclear Sharing in Growth (CNSIG) programme. This programme aims to develop the UK manufacturing supply chain for civil nuclear in new build, operations and decommissioning, and to help UK companies win work in the nuclear industry at home and overseas. It seeks to combine the expertise of manufacturing companies with that of universities, working with companies in the civil nuclear supply chain to help them compete by raising quality, reducing costs and developing new capabilities.
Stainless Metalcraft is a fabrication and machining company based in Cambridgeshire, with capabilities ranging from high specification mechanical design through to project management, manufacture and installation. The agricultural surroundings of the thirteen acre Chatteris site that has been Metalcraft’s home since the late 19th century belie the cutting edge capabilities that have seen the company become the preferred supplier to demanding customers including scientific research facilities worldwide. A Chinese manufacturing facility is devoted to production of high volume customer products, providing a truly global capability.
Metalcraft’s bespoke products are supplied into diverse industries from space and medical to marine and water treatment. The company has a turnover of £14 million and 165 employees who have built a wealth of experience in the design and manufacture of vacuum, cryogenic and pressure vessels – ranging from the largest at over 35m long and 140 tonnes in one piece, to equipment 0.5m in length, 0.5m in diameter and only a few kilos in weight.
At Metalcraft, Adams realised there was a need to realign the business to meet the challenges of demanding customers in the nuclear industry, and to focus on quality and growth, not just cost reduction. He was determined to do this by harnessing the talents of his management team. Metalcraft was one of ten companies signing up to the CNSIG programme, and called upon the expert services of IfM Engage to help identify the key issues and priorities and to develop the business strategy. “It was like having a team of helpers to facilitate this re-alignment”, said Adams.
Working with IfM Engage
IfM Engage’s work was organised into two clear stages: Prioritisation and Strategy Development. Both are rigorous but also flexible according to the demands of the project. The IfM Engage work for Metalcraft had a focus on excellence in process, facilitation and above all, tangible impact.
In the prioritisation stage
Duncan Hurlstone worked with the whole management team, bringing them into common agreement on the challenges, and highlighting the key priorities on which they needed to focus. This stage was delivered rapidly whilst being highly effective and requiring minimum disruption to the management team. A total of a half-day was required from each manager for both interviews and feedback sessions.
As part of prioritisation, a feedback process stage involved the results of these early discussions being synthesised to establish the extent to which the management team was aligned with business priorities, and to begin to form a structured view of prioritised potential improvement paths.
The strategy development stage
This stage consisted of four half-day workshops within a calendar month, delivered by the IfM Engage team, and scheduled to minimise disruption to the business. The workshops helped the team actively to consider a range of potential strategic options, before homing in on a chosen future direction for the company. The fourth workshop focused on the identification and start of key projects that would be required to help Metalcraft on its way.
The workshops identified three growth opportunity areas for Metalcraft: decommissioning, nuclear new build and operations. With this focus, Metalcraft was then better able to capitalise on other workstreams available under CNSIG.
The process was well received within the business. Austen Adams and his team found the robust yet flexible IfM Engage approach highly beneficial.
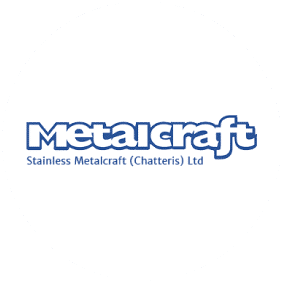
“Bringing the team through this process provided positive endorsement and engagement with the actions. These kinds of processes often end with ‘what you could/should do’; this one leaves you with ‘what you are going to do’ – clear actionable output with ‘buy in’. We have seen a clear tangible impact of the work already.”
Austen Adams
“Excellent facilitation and a very robust process executed quickly and efficiently. Great job.”
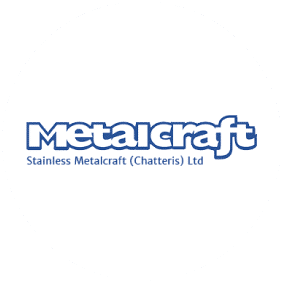
“Bringing the team through this process provided positive endorsement and engagement with the actions. These kinds of processes often end with ‘what you could/should do’; this one leaves you with ‘what you are going to do’ – clear actionable output with ‘buy in’. We have seen a clear tangible impact of the work already.”
Austen Adams
“Excellent facilitation and a very robust process executed quickly and efficiently. Great job.”
About Stainless Metalcraft
Metalcraft is a long-established British manufacturer of high specification stainless steel equipment for some of the world’s most hazardous environments. Its broad expertise spans the design and manufacture of pressure, vacuum and cryogenic vessels and tanks for safety critical applications in industry sectors such as space, medical, marine, research, power generation, oil, gas, petrochemical, waste and water treatment. It produces equipment at all scales, from a 35 metre-long, 140 tonne one-piece tank to vessels of less than 0.5 metres and weighing a few kilos.
The company, which dates back to the 1890s, now employs 160 people at its Cambridgeshire facility in the UK. Metalcraft’s Chinese manufacturing facilities are devoted to production of high volume customer products, providing a truly global capability.