Sustainable innovation: Quick wins in sustainable manufacturing
Sustainable innovation and continuous improvement initiatives
As part of a recent study into sustainable innovation in manufacturing, researchers interviewed practitioners from global manufacturing firms across a range of industries including automotive, aviation, FMCG, and healthcare, alongside subject matter experts in the field of sustainable manufacturing. The study and interviews provided 200 data points that were analysed under 13 headings to reveal the best quick win strategies by using continuous improvement methods. Download the full report for more detail, and join the Sustainability Association for further insights and collaboration with world-leading researchers to drive sustainable changes.
DOWNLOAD THE FULL REPORT
Jump to the bottom of this article to download the full report and receive a checklist of 20 recommendations to improve sustainability performance in your organisation.
Best sustainability strategies practices for rapid improvement
The study identified common themes, patterns, best practices, and critical success factors among businesses that achieved consistent, rapid sustainability improvements, including surface-level assessments of current resources and starting small with low-cost or no-cost improvements. Some of these are outlined below – for the full list download the report.
1. Challenge the idea that sustainability costs money
One of the biggest roadblocks to creating fast sustainable innovation improvements is the belief that sustainability is expensive. In practice, economic and environmental efficiencies are often aligned and businesses can target quick no-cost, low-cost improvements to gain economic flexibility. By conservative estimates, through increasing energy and resource efficiency, the UK stands to gain “£10 billion per annum in additional profit for manufacturers, 300,000 new jobs, and a 4.5% reduction in our total annual greenhouse gas emissions. That’s a 12% profit increase for UK manufacturers without spending any money.” In a stunning sustainability example, Toyota’s UK factory reduced the energy to make one car by 77%. That means Toyota can now make four cars with the same amount of energy it used to make one car in the past. Yet the facility didn’t purchase any expensive equipment to achieve this level of improvement.
2. Quickly assess current resource use
No organisation can improve without understanding its current condition. As part of a sound sustainability strategy, it’s vital to first assess existing resources at a surface level. A deep assessment may be prohibitive due to a lack of measurement and metering tools. However, a simple high-level overview and approximation can supply a workable understanding of overall system performance. Even a surface estimate like this can reveal variations in performance and gain time to deploy more advanced measurement and metering options during future efforts. While identifying current waste may seem trivial, the research shows it’s in fact immensely important. Knowing what a factory is wasting is the first and most vital step toward conservation.
3. Don’t wait for a full sustainability strategy
Use an initial analysis of current resources to guide the creation of a working sustainability strategy aligned with core business values and processes. Set realistic targets achievable in the short term to avoid discouragement and build confidence among employees and managers. At this stage, setting up the right KPIs for the current state of the business can prevent frustrations from not achieving sustainable innovation targets. It can help to start by holding internal discussions on priorities and focusing on well-known issues and impact points. During interviews in the study, companies highlighted opportunities to switch processes and equipment off (As long as it can be switched on and deliver a top quality part easily). Simple steps like putting stickers on equipment to identify if it can be turned off, to more comprehensive controls like having a dedicated energy control strategy for a paint area were given as examples. Reducing energy consumption is not only good for sustainability performance but also reduces costs, so this alignment with key business drivers helps sustainability quickly become mainstream.
4. Include sustainability KPIs
What gets measured gets improved. Monitoring metrics that align with sustainability is key to driving sustainability improvements through continuous improvement. It’s enough to start small with KPIs, selecting a few that track the current sustainability condition in a cell or facility, such as the use of electricity, water, coolant, or the volume of materials waste. It’s important to share these metrics often (ideally in real-time) with key stakeholders, especially on the shop floor, so they can also seek improvements and start to drive them KPIs in the right direction.
5. Start small
What gets measured gets improved. Monitoring metrics that align with sustainability is key to driving sustainability improvements through continuous improvement. It’s enough to start small with KPIs, selecting a few that track the current sustainability condition in a cell or facility, such as the use of electricity, water, coolant, or the volume of materials waste. It’s important to share these metrics often (ideally in real-time) with key stakeholders, especially on the shop floor, so they can also seek improvements and start to drive them KPIs in the right direction. A simple yet effective approach teams can look at straight away is to review resource variation – the difference between energy used on good days and bad days. Teams can identify ideas and processes that have already been proven to work as they have ‘been done before’. One organisational sustainability example achieved over 15% improvements remotely by identifying and acting on performance variation in annual production and resource data.
How Small?
From responses and examples gathered during interviews from the study, rapid sustainability improvements are defined as:
“No-cost/low-cost, short-term, and iterative improvement activities as a part of a long-term sustainability plan with a ROI and/or ROC of 6 months or less”
Download the report ‘Driving resource efficiency through rapid sustainability improvements’ and you’ll also receive a checklist of 20 ways you can improve sustainability performance in your organisation.
6. Create a new perspective of sustainable innovation
Businesses in the study have benefited from having a fresh pair of eyes on site. Bringing in someone who is less familiar with the process avoids “we have always done it this way” thinking and permits the freedom to question. This “outside of the box” approach can often introduce simple solutions and rapid sustainable innovation improvements. It can create a situation where factory managers think, “We have been passing in front of that for 10 years and why haven’t we thought of that?” In one organisation, an operations leader was surprised to see leading organisations in the sector were often achieving 5-8% efficiency improvements each year. They considered this a high target, hence sought external expertise that enabled the team to see their organisation through a fresh perspective, resulting in a range of new ideas for potential improvements.
7. Rely on existing CI skills and tools
The companies that applied existing continuous improvement tools experienced the least difficulty in implementing sustainability innovation. Businesses that already have a culture of continuous improvement in place should leverage that success to shift to using CI tools for sustainability.
The research found that refocusing traditional lean tools on sustainability led to impressive ROI in as little as a few weeks to a few months. Existing lean tools that can be used for sustainability include DMAIC (define, measure, analyse, implement and control), TPM, TQM, benchmarking, six attitudes (Toyota), and the fresh eyes approach.
As a first step, companies can make the shift from traditional CI to sustainability CI by adding a sustainability objective to their existing quality, reliability, and productivity targets. It’s vital for top management to support and clearly communicate the sustainability transformation.
Businesses without an existing continuous improvement capability can start building it with sustainability in mind to obtain production systems that are both efficient and sustainable.
Although any organisation can achieve quick wins in sustainable manufacturing through continuous improvement, efforts will be successful to the degree that a business has progressed along its CI journey. Organisations that already use traditional tools like Lean Manufacturing, Total Quality Management, and Total Productive Maintenance possess the maturity required to reap significant and rapid sustainability benefits.
Critical success factors in sustainable strategy examples
The research identified several critical success factors in achieving an environmental and sustainable working practice, as well as a few important barriers to overcome. Success with sustainability through CI comes down to people, with relationships, trust, communication, and recognition first and foremost.
Data quality, quick action, CI competence, and supporting employees with time to make improvements and with small budget allocations also play a central role. Here are the key sustainability success factors and barriers:
Critical Success Factors | Sustainable Innovation Barriers |
|
|
|
|
|
|
|
|
|
|
|
|
How do sustainability practices benefit businesses?
Increasingly, sustainability is moving from a “good idea” to a necessary part of doing business. As energy and materials costs see 10% to 30% annual inflation rates, continuous improvements in sustainability can be the difference between thriving and closing up shop.
Sustainability drives innovation and can also improve an organisation’s reputation with its customers, as growing numbers of consumers put sustainable shopping and the environment high on their list of priorities.
Summary
Sustainability in manufacturing can drive production processes towards minimised material inputs, waste management, increased energy efficiency, reduced water usage, and improved efficiency in land usage.
Deep research by the University of Cambridge Institute for Manufacturing suggests that using a set of key continuous improvement initiatives can achieve sustainability improvements rapidly, improve resource efficiency, and contribute to overall firm sustainability.
You can learn more about the critical success factors for implementing environmentally sustainable business practices by joining the Institute for Manufacturing’s Sustainability Association, where you’ll be empowered by the right knowledge, the right expertise, and the right network to accelerate innovative sustainable solutions in your organisation.
DOWNLOAD THE FULL REPORT
This report investigates the role of continuous improvement initiatives in achieving rapid sustainability improvements and driving resource efficiency.
Reasons to download this report:
– Discover some of the ways manufacturers successfully achieve rapid sustainability improvements
– Understand some of the success factors and barriers in progressing sustainability initiatives
– Receive a checklist with 20 recommendations to support you in using continuous improvement initiatives to drive resource efficiency
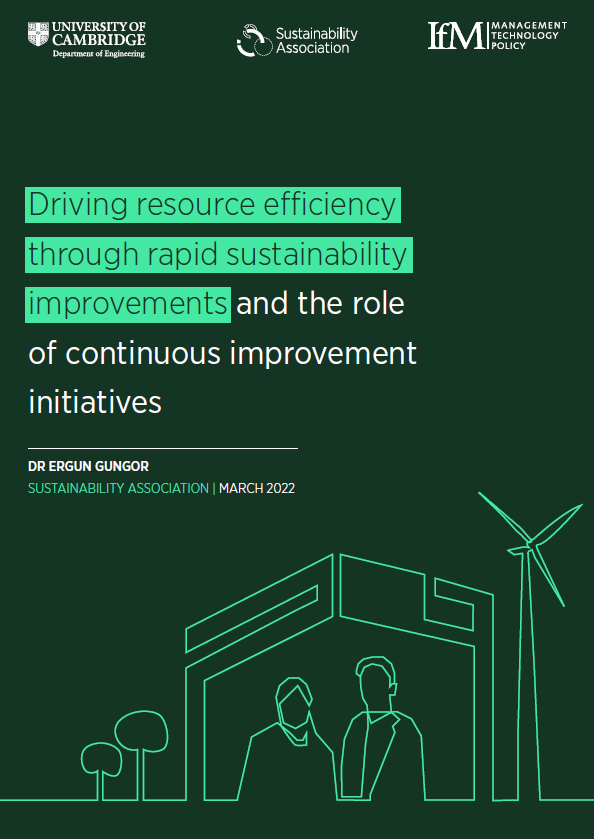
This report is an output from the Sustainability Association.
The Sustainability Association is a membership group designed to allow manufacturing leaders to work together to identify and overcome common challenges in making their operations more sustainable.
In collaboration with world-leading researchers in the field and talented peers from different industries, the Association provides member companies with the right knowledge, right expertise and right network to accelerate sustainable change in their organisation.