Driving sustainability success at Kenyan tea factories
EASTERN PRODUCE, PART OF CAMELLIA PLC
Impact

IfM tools and strategies are integrated in the day-to-day operations of the tea factories and continue to minimise energy usage
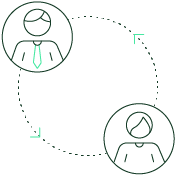
Workers on the factory floor experience ownership of the company’s sustainability work, which has boosted morale and given a sense of shared direction
Impact

IfM tools and strategies are integrated in the day-to-day operations of the tea factories and continue to minimise energy usage
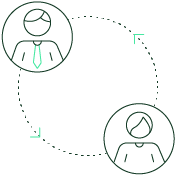
Workers on the factory floor experience ownership of the company’s sustainability work, which has boosted morale and given a sense of shared direction
The challenge
Kenya is one of the world’s biggest producers of tea. The sector employs over 600,000 smallholder farmers, supporting over three million people. But drying, grading, and packaging mean tea production is highly energy intensive. To produce one kilogram of tea requires approximately 3‐6 kWh of thermal energy — supplied mainly from wood combustion — and 0.2‐0.5 kWh of electrical energy from grid and diesel generators.
In 2020, Eastern Produce Kenya (EPK), one of the country’s largest tea producers and exporters, invited IfM to apply the ‘Cambridge Sustainable Improvement Method’ (CSIM)’ to help re-focus their efforts on reducing the amount of energy used at their Chemomi and Kepchomo tea factories.
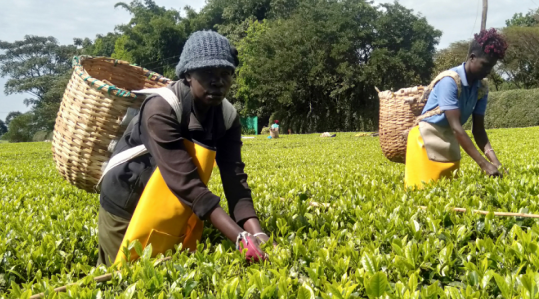
The approach
Through online meetings and workshops over 12 months, the team worked with EPK to identify where energy could be saved and how to make sustainability relevant and understood by the factory workers.
Some of the straightforward actions immediately impacted firewood and electricity improvements. “Because woodpiles reduce wasteful moisture in fuel,” Gary Punter, Industrial Associate at IfM Engage, explains, “we suggested improving firewood storage by expanding covered wood storage areas. Steam usage was also reduced by eliminating steam leaks and reducing dust from radiators and heat exchangers. We also helped develop an energy dashboard to delve further into withering and drying.
“To reduce electricity, we encouraged the simple actions of switching off lights & sockets and using natural lighting instead. At Chemomi, this has reduced consumption by 25%.
In addition, we suggested tea reworking to avoid additional re-processing energy, which damages KPIs and segregates dry and moist areas for the better withering of green leaf.”
Gary explains that one of the key success factors was getting the local team engaged in the changes and making the sustainability gains relevant to their context.
“We engaged the factory workers on their terms and in their language. We did this by converting energy into something recognisable, not gigajoules, but ‘how many cows can you buy with the savings?’ This gave us all a laugh but effectively equated to how much energy had been saved. It brought understanding to the room – that energy wasn’t something intangible. By the end of the project, they worked out that they had saved 2,000 cows – the size of the President’s herd!”
Gary recognises that local efforts were mirrored by a strong commitment from EPK HQ to try something new, as well as supportive managerial and technical leadership on the ground in Kenya:
“The open and positive culture of the Kenyan factory management and factory staff, coupled with our empathy and understanding of ‘real’ factory challenges and simple methodology, meant we could see impactful changes almost immediately.
“This wasn’t about us coming in and telling them what they need to do, then leaving. EPK had already been engaging in various energy-saving activities. This was about walking alongside them, listening to them, and getting them involved.
“For example, we encouraged the leadership team to establish their targets, to establish local Improvement teams to undertake surveys and implement their action plans and provide recognition for all the hard work involved.”
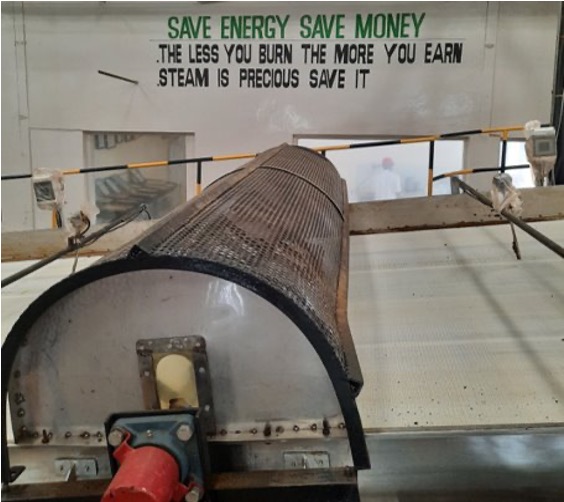
Simple steps = significant change
Some of the steps involved in implementing CSIM include:
- Focus on energy KPI data for the good energy days.
- Engage the leadership team to establish their own targets.
- Engage factory staff to identify top energy users.
- Local improvement teams undertake surveys and develop visual management.
- The local teams develop and implement their own action plans. Local ownership makes the impact of the programme long-lasting.
- Review of plans focusing on KPI trends. Use of a dashboard implemented to ensure that improvements stick.
- Recognition for the hard work of all involved!
The results
After 12 months, teams reported a 15-30% reduction in thermal and electric energy consumption at both sites. There was also a significant increase in tea produced per unit of fuel (kWh/m3).
“Now, there is the controlled start-up of machines after a power outage,” says Chris Ballard, EPK’s Technical Director. “No machines are left idle or running when not in use. There is also proper work output by employees who now understand that their work has a direct impact on energy savings. The shop floor teams appreciate the load-shedding regime and no longer see it as a limiting factor in withering operations”.
“We have also adopted a new way of covering firewood in the yard resulting in high firewood utilisation efficiency compared to previous years. Data on electrical energy use is collected from each section of the factory. The data is compared between all factories, and this highlights inefficient sections of a factory that must be improved”.
“These actions have led to significant energy savings at both sites, and there has been an overall improvement of factory performance across all areas,” says Chris.
“Since working with IfM, everything we implemented has been continued. Shop floor workers now own the energy-saving culture. Some team members have now moved to other factories and are implementing these ideas in these factories. So, the ideas and what we have learnt are spreading. We’re working together effectively and committed to bringing our customers tea that has a minimal impact on the environment.”
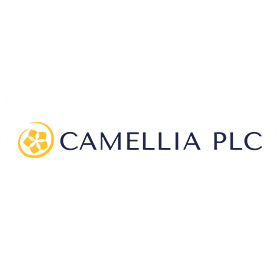
“Since working with IfM, everything we implemented has been continued. Shop floor workers now own the energy-saving culture. Some team members have now moved to other factories and are implementing these ideas in these factories. So, the ideas and what we have learnt are spreading. We’re working together effectively and committed to bringing our customers tea that has a minimal impact on the environment.”
Chris Ballard, Technical Director, Eastern Produce Kenya, part of Camellia PLC
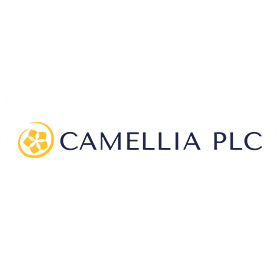
“Since working with IfM, everything we implemented has been continued. Shop floor workers now own the energy-saving culture. Some team members have now moved to other factories and are implementing these ideas in these factories. So, the ideas and what we have learnt are spreading. We’re working together effectively and committed to bringing our customers tea that has a minimal impact on the environment.”
Chris Ballard, Technical Director, Eastern Produce Kenya, part of Camellia PLC
FIND OUT MORE
Find out more about the Cambridge Sustainable Improvement Method, and how it could make a sustainable impact in your organisation.
About Eastern Produce Kenya
Eastern Produce Kenya Ltd (EPK) is one of the biggest multinational producers of tea in Kenya, with tea estates in the Nandi Hills area, west of the Great Rift Valley.
Through investment in the land, factories and human resources, EPK produces some of the highest quality teas in Africa in a sustainable way with particular emphasis on modern agricultural practices, improving factory energy efficiency, increasing use of renewable energy and reduction in carbon dioxide emissions.
Eastern Produce Kenya Limited is part of the Camellia Plc group that has agricultural and horticultural operations in Kenya, Tanzania, Malawi, South Africa, India and Bangladesh.
IfM contributors to this project
Professor Steve Evans, Gary Punter, Ian Bamford, Saul Jones