Reducing waste in manufacturing
Making new products requires a lot of materials and energy, so manufacturing waste is inevitable in almost any business.
This article explores how to reduce waste, showing that it is possible to also generate additional value in doing so.
Drawing on evidence and research from the Institute for Manufacturing, the article will:
- Explore the main benefits of reducing manufacturing waste.
- Discuss how to convert waste into value using a circular economy approach.
- Present tools, techniques and practices that work such as how to use data to find ways to eliminate waste.
- Use a case study demonstrating sustainable plastic manufacturing.
FREE Report: Driving resource efficiency through rapid sustainability improvements
Download a study into rapid sustainability improvements, including a 20-stage checklist on steps you can take to accelerate sustainability in your organisation.
What do we mean by waste?
Waste isn’t just what goes in the recycling bin. There are many types of hidden wastes that can hamper the efficient use of resources within an organisation.
Considering all types of waste from across the factory – also called a ‘lean’ approach, means that you can start to look at waste so it includes everything from time to inventory, including waste of:
- Overproduction
- Time on hand
- Transportation
- Processing itself
- Stock at hand
- Movement
- Making defective products
- Underutilised workers
At the IfM, we have developed a technique of analysing manufacturing waste that puts every source of waste into the context of the whole production system.
As discussed in this webinar, we work with a number of companies to help them find ways to eliminate waste. One technique uses existing factory data (for example, invoices and bills of materials) rather than relying on the implementation of an expensive monitoring system. This way, companies can focus on improvements where they are needed most; and on things that will drive value and enthusiasm from the workforce.
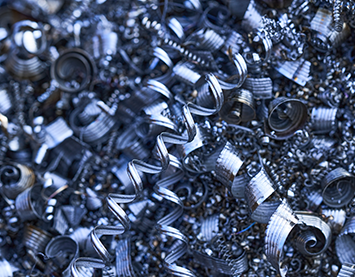
What are the benefits of reducing waste?
Research from the IfM calculates that if every factory in a sector moved towards optimum sustainable performance, there could be 24% profit gained, 30% more jobs generated and 9% less greenhouse gases shared across that sector.
Shifting from methods of waste disposal to processes of waste reduction can bring a range of benefits of reducing waste including:
- Increased profit by saving money through the more efficient use of raw materials, packaging and technology.
- Improved reputation among customers, suppliers, potential employees and insurers.
- Greater environmental responsibility makes it easier to meet environmental standards and regulations.
There are huge benefits to be gained by embarking on a journey to reduce manufacturing waste. For example, using lean principles, one jeans factory was able to reduce the amount of water they used to make each pair of jeans from 800 litres to less than 1 litre.
How to increase interest in reducing manufacturing waste
It can be daunting to begin a sustainability journey in your organisation.
Firstly, you need to ensure the alignment of sustainability with key issues. Consider what your key business drivers are for growth and risks. It does take time, but if you engage the leadership of your business and demonstrate that sustainability can positively influence those key drivers, you should find support.
Next, you need to get people involved from across the organisation. There are four levels of activities that people can get involved with:
- Engage and get the most of what you have now with minimal investment.
- Get technical and optimise – technology, especially digital, can be a massive facilitator of sustainability.
- Use investment to increase efficiency – this can result in quick wins but requires confidence and the right management and delivery skills.
- Innovate to transform your business and supply chain – think across sectors. For example, one company’s waste is another company’s raw materials for new products!
When people begin to engage, make sure you track your sustainability results to the bottom line and talk about your success stories to build your sustainability brand within your business.
Creating sustainability momentum that endures will test a wide range of skills, so don’t be afraid to seek help!
How can manufacturers generate value whilst reducing waste?
Learning from some of the companies that have excellent continuous improvement programmes, we have found that they have followed these four steps successfully:
- Find the 4 biggest impacts – these will most likely be related to energy, water and waste.
- Start by asking simple questions – ask simple questions such as ‘On which day of the week do we use the least energy and why?’ to start your sustainability journey.
- Use your normal processes – once you have identified the waste, use your standard techniques for continuous improvement.
- Widen the search for value – begin to move outside of the direct manufacturing processes.
Featured solution: Cambridge Sustain 8
Cambridge Sustain 8 is an organisational engagement programme focused on making significant sustainability improvements with minimal investment. By bridging the gap between corporate objectives and sustainable practices on the factory floor, this approach has been successfully implemented in numerous factories, yielding measurable savings within just one year of implementation.
How to reduce manufacting waste – three case studies
Seeing the ‘hidden’ waste is an important part of waste identification, but without being able to value that waste, it can be hard for companies to build a case for action and difficult to get the team on board.
At the Centre for Industrial Sustainability in the IfM, we have developed tools and methods to support resource efficiency. The three case studies below outline examples of how these tools have helped organisations reduce manufacturing waste in practice.
Case study one: Reducing plastic waste
The IfM’s Zero Loss Yield Analysis (ZLYA) tool helps manufacturers to identify hidden losses by using existing data streams and putting waste value into the context of the business as a whole.
The results from this approach are often very illuminating. One manufacturer we worked with to reduce plastic waste, discovered that their actual waste was 14 times greater than they had thought. Using this approach uncovered all sorts of underlying problems within the factory including the imbalance in the production system.
The factory, which produces plastic products by using injection moulding believed they were only rejecting 1% of their main product (plastic coffee capsules which comprise of a cup and a lid). Based on their ‘reject rate’, they thought they had a 99% yield. But when looking at what was actually happening, the waste was 14 times that amount. They also discovered there was a major imbalance in product production. They produced 14m capsules and 16m lids – so a 2m surplus waste of materials.
Case study two: Working with communities to recapture value from waste
In Thailand, a project used local industrial and ocean plastic waste alongside local community knowledge and commitment to develop sustainable products and services and identify circular economy business opportunities for local entrepreneurs.
Thailand, which is one of the biggest ocean plastic polluters in the world, has limited waste management systems, combined with very high consumption of plastic packaging, and a lack of awareness of the toxic impact of littering.
This grass-root circular economy case study shows how one project created momentum to address waste problems at a local level, and an understanding of how to generate real business ideas from the circular economy.
Case study three: Discovering ways to eliminate waste at a sugar factory
Anticipated changes to the European Union (EU) Common Agricultural Policy and the need to stay competitive within the EU, inspired the British Sugar plant in Wissington to evaluate step changes in its manufacturing approach.
The factory looked at all waste streams to become a no-waste biorefinery; successfully building on the core business to utilise all co-products and wastes.
After consolidating plants and expanding capacity at its Wissington facility, they successfully implemented a combined heat and power plant. This simultaneously increased the factory’s financial efficiency and its capacity to expand beyond sugar production.
Revenues are generated by the sale of co-products, and costs are avoided by sending less material to landfill. Wissington is now the most efficient beet producer in Europe. Read more on the AB Sugar case study here.
Manufacturing waste webinar
You can hear more about examples of waste reduction, including how to reduce waste in concrete processes, in our webinar: ‘Manufacturing sustainability: Identifying and eliminating waste’.
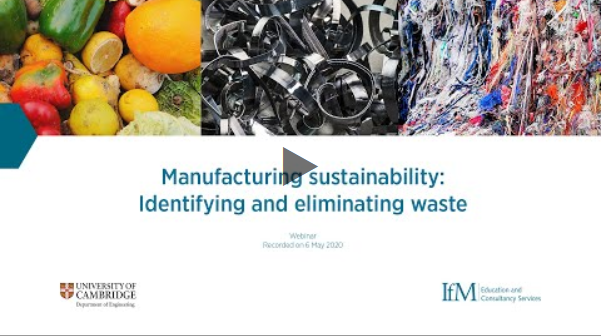
Future research: circular bioeconomy centre (CBC)
At the IfM, we are looking at how we can take lessons from successful case studies (such as the Wissington sugar factory) and are in the process of seeing up a Circular Bioeconomy Centre.
The Centre will look at co-creating new value chains involving farmers, processors, retailers, policy makers and citizens to develop solutions to deconstruct all imported waste biomaterial; giving the whole of the UK a national plan for a Zero Waste Bioeconomy.
To find out more or to get involved with the Centre, don’t hesitate to get in contact.
If you are trying to create a plan when you have not travelled this road before, why not consider joining the Sustainability Association, where you can get together with others going on the same journey and learn from those who are already ahead.
You can also draw on the Cambridge Centre for Industrial Sustainability’s extensive research. The Association will provide training, tools and practical leadership support to enable businesses to progress sustainability initiatives.
Sustainability support services
Consultancy
services
Our highly experienced industrial associates look at how your business operates to uncover ways you can think and act differently to be more efficient and sustainable. We work in partnership with you, sharing world-class research, tools, and techniques in practice.
Sustainability
Association
Established by leaders at the IfM, the Sustainability Association is a community of global manufacturers, researchers, and experts that regularly meet to provide the inspiration, insights, and practical support needed to bring immediate sustainable change.
Sustainability support services
Consultancy services
Our highly experienced industrial associates look at how your business operates to uncover ways you can think and act differently to be more efficient and sustainable. We work in partnership with you, sharing world-class research, tools, and techniques in practice.
Sustainability Association
Established by leaders at the IfM, the Sustainability Association is a community of global manufacturers, researchers, and experts that regularly meet to provide the inspiration, insights, and practical support needed to bring immediate sustainable change.